Crawley-based hydrogen fuel cell inventors Bramble Energy secure £35million funding
and live on Freeview channel 276
With Covid about to put a stop to their research, they piled their equipment into a car and set up a temporary lab in a garage in Sussex.
This was the catalyst behind the explosive growth of Bramble Energy. The company, based in Crawley, is developing new types of hydrogen fuel cells which can be used in many different vehicles and portable power units. “We were following up on a research project by UCL and Imperial College back in 2012 which had won the Carbon Trust’s Fuel Cell Polymer Challenge. We were working on proof of concept and development and were basically just squatting in a lab at UCL,” explained COO Vidal Bharath.
Advertisement
Hide AdAdvertisement
Hide Ad“We were finding out how to mass manufacture fuel cells at low cost. Then Covid hit, and threatened to shut us down, so I got up in the middle of the night and drove all our equipment to Tom’s place in Sussex, where we had to quickly make his garage ‘hydrogen safe’,” Vidal laughed.
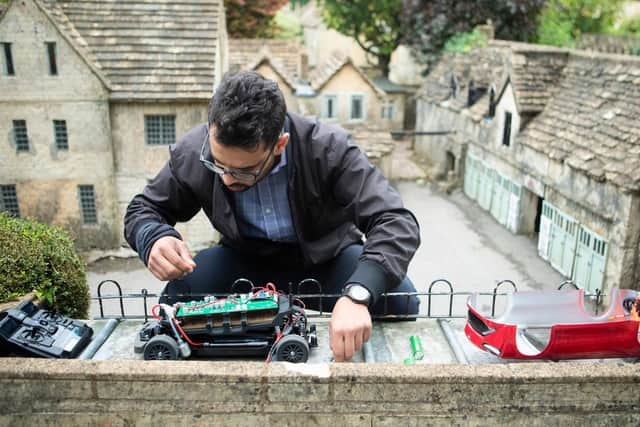
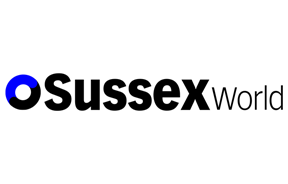
He and his colleagues Tom Mason and Erik Engebretsen had already raised £600K from venture capitalists in 2018 and were on the verge of securing another £5M.
Hydrogen fuel cells, or stacks, work by passing compressed hydrogen through a catalyst material to separate hydrogen molecules into protons and then, using a few other processes, electrical energy. Up to now making the stacks has been expensive. The units are traditionally made using specialist manufacturing techniques, with bespoke tooling needed to stamp out metal plates containing the catalyst. This is an expensive and slow process.
“Our technique uses PCB laminates - the green printed circuit boards you can imagine inside most electronic equipment. These are made everywhere and can be ordered to scale within weeks to any size or shape in large or small quantities. We then dip the PCBs in the catalyst, known as a membrane electrode assembly, or MEA, and assemble the stacks here - we’re really just glorified plumbers.
Advertisement
Hide AdAdvertisement
Hide Ad“Our USP is our adaptability in form factor, lower cost - we don’t need factories - and the system is more scalable than anyone else’s.
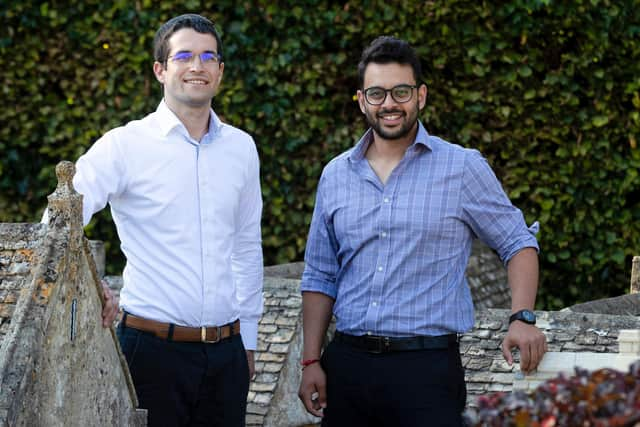
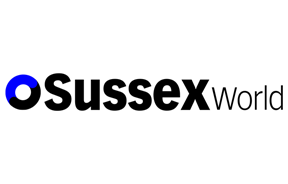
“Our stacks also use plastic rather than metal end-plates so are much lighter. This means they can be used in many different applications. They don’t even have to all be in one place, meaning they could be spread out across a vehicle for better weight distribution. Having more stacks could also give more built-in redundancy.
“We’re currently working on a range-extending battery pack for electric vans with Mahle Powertrain and we’re also talking with Renault and Nissan. And we can see applications for cars, forklifts, planes, trains and ships - we’ll be testing one in a narrowboat soon.
“The system can be used wherever a battery is used for power. We just mate the fuel cell to it. The stack constantly trickle-charges the battery,” explained Vidal.
Advertisement
Hide AdAdvertisement
Hide AdBramble moved out of Tom’s garage into a 5,000 sq ft unit not far from Gatwick Airport in July 2020. “We use a PCB supplier in Scotland so being close to the airport is important to us,” said Vidal. By the following May they doubled their size when they took on the neighbouring unit. They currently employ 50 full-time staff and have just signed a lease for an additional 35,000 sq ft building. “It’ll be used for offices and a mix of research, production, R & D and testing.
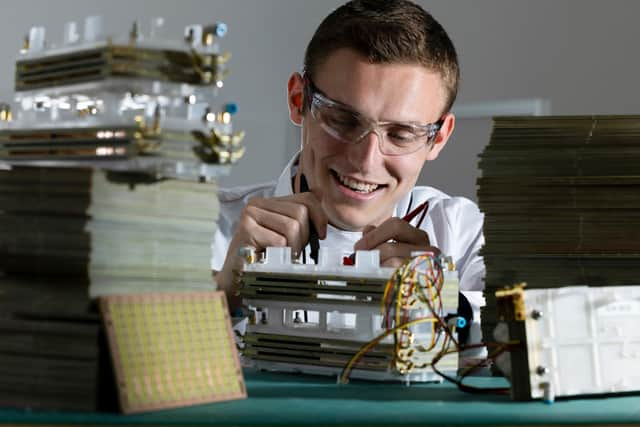
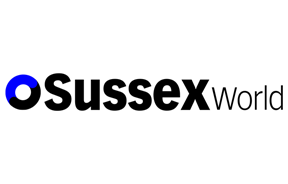
“Last year we made a miniature hydrogen powered Toyota Mirai Tamiya remote control car. And we’ve just finished another 100 for Tamiya.
“Our stacks are also being fitted into portable power units. They can replace diesel generators, and can run silently for 30 days. To get the same power from one 20kg cylinder - with 0.4kg of hydrogen in it, you’d need the equivalent of a quarter tonne lead acid battery or an 80kg lithium ion battery.
“We received a £35M equity release led by Hydrogen One Capital Ltd in February. This is helping us to roll-out our portable energy products and get our mobility fuel cells certified for each sector.
Advertisement
Hide AdAdvertisement
Hide Ad“We’ve just started work on a skunkworks project - it’s electrochemistry on acid. We’re making an electrolyser to make hydrogen. So in the future a haulage company may put in an order for a fuel cells and truck refueling facility too.”